مشخصات فنی مهندسی فرآیند تولید فولاد
دیسیپلین های مختلف مهندسی کارخانه فولاد
جهت انجام مهندسی کامل یک کارخانه تولید فولاد معمولا، واحد / بخش / دپارتمان / دیسیپلین های ذیل را می توان نام برد.
فرآیند (عمومی و تکنولوژی)، نسوز، مکانیک، سیویل، سازه، معماری، پایپینگ و سیالات، برق، ابزار دقیق و اتوماسیون

- واحد فرآیند شامل فرآیند عمومی و فرآیند تکنولوژی: طراحی و مهندسی فرآیندها، جانمایی کارخانه، چیدمان تجهیزات، عایق و رنگ
- واحد نسوز: طراحی و مهندسی مواد نسوز، مشخصات فنی مواد نسوز، نقشه چیدمان و جزئیات مواد نسوز
- واحد مکانیک: طراحی و مهندسی تجهیزات ثابت، تجهیزات دوار، سیستم حمل مواد، ماشین آلات، بالابرها و غبارگیرها
- واحد سیویل، سازه و معماری: طراحی و مهندسی سازه های فلزی و بتنی، فونداسیون ها، ساختمان های عمومی، محوطه سازی و تاسیسات محوطه، نقشه برداری، توپوگرافی و مكانیك خاك
- واحد پایپینگ و سیالات: طراحی و مهندسی سیستم های لوله كشی، گازهای صنعتی، تهویه مطبوع، آتش نشانی، تصفیه آب و آبرسانی، جمع آوری، تصفیه و دفع فاضلاب و سوخت رسانی
- واحد برق: طراحی و مهندسی شبكه و پست برق، سیستم توزیع برق، رله و حفاظت کاتدی
- واحد ابزار دقیق و اتوماسیون: طراحی و مهندسی سیستم های اتوماسیون و ابزاردقیق
اهم تجهیزات اصلی در واحدهای صنعت فولاد به تفکیک هر کارخانه به شرح ذیل معرفی می گردند.
- واحد کنسانتره
- خط سنگ شکنی: تجهیزات سنگ شکن فکی یا ژیراتوری، سنگ شکن های مخروطی، سرند گریزلی، صفحات تغذیه کننده
- بستر همگن سازی: انباشت کننده، برداشت کننده
- خط تولید کنسانتره: آسیاب غلطکی، هیدروسیکلون، آسیاب گلوله ای، پمپ ها، جدا کننده های مغناطیسی
- واحد آبگیری: فیلترهای نواری مکنده
- واحد انتقال محصول: انباشت کننده، برداشت کننده
- واحد گندله سازی
- واحد انبار مواد اولیه: آسیاب غلطکی فشار بالا، انباشت کننده، برداشت کننده
- واحد آسیاب آهک: آسیاب غلطکی
- واحد آسیاب سنگ آهن: دستگاه تولید گاز داغ، آسیاب های گلوله ای
- واحد مخلوط سازی: دستگاه¬های میکسر اولیه و ثانویه
- واحد تولید گندله خام: دیسک¬های گندله¬ساز
- واحد پخت گندله: بر حسب پروسه تولید تجهیز اصلی این واحد از نوع کوره شبکه متحرک یا کوره دوار یا کوره عمودی می¬باشد
- واحد سرند محصول: سرند ارتعاشی
- واحد انتقال محصول: انباشت کننده، برداشت کننده
- واحد احیاء مستقیم
- سیستم انتقال گندله و محصول: انباشت کننده، برداشت کننده، نوار نقاله
- واحد تولید گاز احیایی: گاز شکن
- واحد احیاء سنگ آهن: کوره احیاء مستقیم
- واحد بازیابی حرارتی: بازیاب حرارتی، دودکش، دمنده¬ها
- واحد فولاد سازی
- سالن ذوب: کوره قوس الکتریکی، کوره پاتیلی، ماشین ریخته گری مداوم، سیستم انتقال مواد فروآلیاژ و افزودنی ها، سیستم انتقال مذاب
- واحد تولید اکسیژن: کمپرسورهای اکسیژن و نیتروژن، ستون تبرید، مخازن ذخیره
- واحد غبارزدایی: فن های اصلی، سیستم خنک کننده، واحد مکش
- تصفیه خانه آب: پمپ ها، فیلترهای شنی، مبدل¬های حرارتی، سیستم اسمز معکوس، واحد تزریق مواد شیمیایی
- واحد تولید هوای فشرده: کمپرسورها، خشک کن هوا
- واحد نورد
- واحد تولید میلگرد و مقاطع فولادی: میز شارژ بیلت، کوره پیش گرم کن، استندهای اولیه، استندهای میانی، استندهای پایانی، بستر خنک کننده، قیچی ها، سیستم بسته بندی محصول
لازم به ذکر است که واحدهای جنبی از جمله سیستم تامین آب خام، آب آشامیدنی، آب پروسس و آب آتش نشانی، تصفیه خانه آب، ایستگاه تامین گاز و سیستم هوای فشرده نیز در تمامی کارخانجات صنایع فولاد، حائز اهمیت بوده و بایستی در زمان مهندسی به آنها توجه ویژه ای نمود.
روش های تولید فولادخام
تقریبا فن آوری های مورد استفاده در تولید محصولات فولادی در مراحل بعد از به دست آوردن تولید فولاد مذاب یعنی ریخته گری و نورد، کم و بیش یکسان است، اما برای به دست آوردن فولاد مذاب از فن آوری مختلف می توان استفاده کرد.
روش ها
- تهیه آهن خام یا چدن مذاب در کوره بلند (BF) و تولید فولاد در کانورترهای اکسیژنی
در این روش از کک به عنوان تولید کننده گازمنواکسید کربن استفاده می گردد از کک در کوره های بلند برای تامین گرمای لازم استفاده می شود همچنین در واحد آلگومراسیون یا کلوخه سازی کنستانتره ها را بهم چسبانده و به عنوان تولید کننده گاز نیز استفاده می گردد از سنگ آهک و آهک موجود در آلگومره به عموان گداز آور برای ذوب Sio2 و ایجاد سرباره ای روان استفاده شود. محصول اصلی کوره بلند چدن مذاب است که برای تیدیل آن به فولاد به قسمت فولاد سازی ارسال می شود.
- احیای مستقیم سنگ آهن (DR) و ذوب آهن اسفنجی (ِِDRI) و قراضه (Scrap) در کوره های الکتریکی از قبیل قوس الکتریکی (EAF) نظیر فولاد خوزستان با القایی (IMF)
مراحل تولید فولاد
نظر به اینکه اکثر سنگ های معدنی آهن دار پس از انفجار و برداشت از معدن بصورت قطعات بزرگ می باشند باید آنها را با سنگ شکن های فکی و یا مخروطی خرد و به ابعاد کوچکتر از 25 میلیمتر رساند. این سنگ ها پس از سرند شدن به دو بخش کمتر از 25 تا 10 میلیمتر برای شارژ کوره بلند و 10 تا صفر میلیمتر برای آگلومره (کلوخه) مورد استفاده قرار می گیرد. و در صورت نیاز به افزایش عیار سنگ آهن و تولید کنستانتره از آسیاب های گلوله ای یا میله ای به زیر 4% استفاده می شود.از کنستانره برای تولید گندله استفاده می گردد.
روش های فراوری سنگ آهن
فراوری سنگ آهن یکی از مهمترین فرایندهای زنجیره تولید فولاد است. فراوری سنگ آهن بر اساس محصول تولیدی:
- تولید سنگ آهن دانه بندی شده
- تولید کنستانتره سنگ آهن
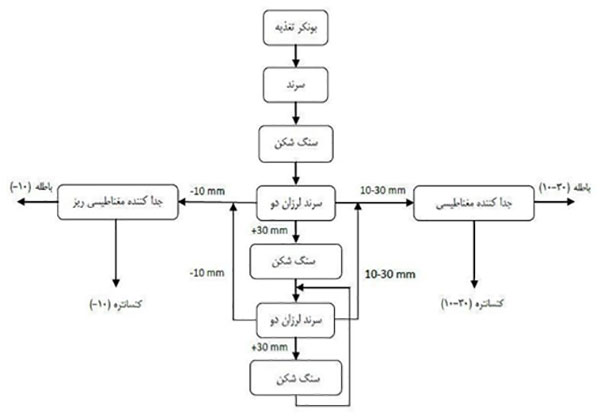
روش استخراج سنگ معدن و انجام عملیات بستگی به نوع کانی، درصد تخلخل و همچنین روش تولید ( کوره بلند یا احیاء مستقیم ) دارد.
واحد کنستانتره سنگ آهن
- عملیات خردایش
اولین مرحله در کارخانه با ورود ماده معدنی به سنگ شکن (کلی یا ژیراتوری) آغاز می شود. در ورودی سنگ شکن سرند ثابت گریزلی نصب می شود که روزنه های آن برابر با ابعاد محصول خروجی از سنگ شکن هستند. سپس مواد معدنی خرد شده با نوار نقاله وارد مرحله بعدی سنگ شکن و سرند می شوند.
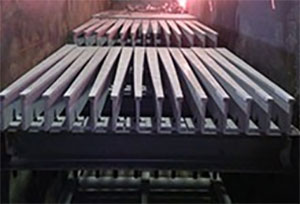
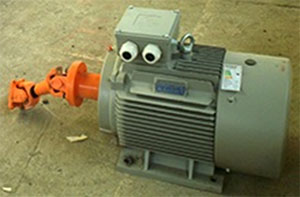
سرند گریزلی
برای طبقه بندی مواد دانه درشت مورد استفاده قرار می گیرد و حد جدایش آن 300 تا حداقل 20 میلی متر است. ظرفیت آن در واحد سطح نیز زیاد است و بستگی به فاصله شبکه ها از هم دارد و ممکن است به 1000 تن در ساعت به ازای هر متر مربع از سطح سرند بالغ شود. بیشترین کاربرد این نوع سرند در کانه آرایی،طبفه بندی بار اولیه در مرحله باردهی به سنگ شکن اولیه است به این ترتیب بخشی از بار اولیه که دارای ابعاد بزرگتر از حد مجاز برای سنگ شکن است، از آن جدا می شود و از گیر کردن آنها در دهانه ورودی سنگ شکن جلوگیری می کند و یا قطعاتی که دارای ابعاد کوچکتر از گلوگاه سنگ شکن هستند از آن جدا شده، باعث افزایش ظرفیت سنگ شکن و کاهش فرسایش آن می شود.
- آسیاب
مواد معدنی با ابعاد کمتراز 30 میلیمتر، به منظور خردایش بیشتر وارد مرحله آسیاب می شود که بصورت ترانجام می پذیرد. در این مرحله، مواد توسط آسیای خودشکن یا نیمه خودشکن و یا آسیای غلتکی فشاری تا اندازه 1-5/0 میلی متر آسیاب می شوند. در این قسمت ها که خردایش در محیط تر انجام می پذیرد، ابعاد خردایش توسط هیدروسیکلون ها کنترل می گردد. و هدایت مواد که در آب شناور هستند و ترکیب دوغاب (اسلاری) را ایجاد کرده اند، توسط پمپها انجام می شود.
تجهیزات سنگ شکن فکی
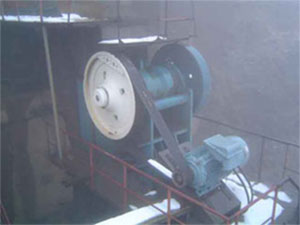
تجهیزات سنگ شکن مخروطی
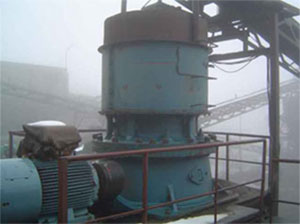
- پرعیارسازی
ذرات پس از عبور از مرحله آسیا کنی به ابعاد بسیار ریز مورد نظر رسیده اند و لازم است به منظور جدا کردن مواد باارزش از ترکیبات باطله داخل اسلاری، وارد مرحله بعدی شوند. اسلاری توسط پمپ به مرحله جدایش مغناطیسی هدایت می شود. جداکننده های مغناطیسی تر، عموماً جداکننده های نوع درام هستند.
- آبگیری
سنگ آهن پرعیار شده حاوی مقادیری آب است که باید آبگیری و خشک گردد و رطوبت آن به 10-9 درصد برسد. بدین منظور از فیلترها برای جدایش آب کنسانتره بدست آمده، استفاده می شود. سپس کنسانتره آبگیری شده به انبار محصول منتقل و در آنجا دپو میگردد. باطله نیز برای آبگیری به سمت تجهیزاتی بنام تیکنر هدایت می شود. در آنجا مواد جامد تهنشین شده و آب بصورت سرریز از بالای تیکنرخارج می شود. ذرات جامد ته نشین شده نیز توسط بازوی جمع کننده کف تیکنر به سمت مرکز هدایت و توسط پمپ به سمت سد باطله هدایت می شوند.
جدا کننده مغناطیسی خشک و تجهیزات آن
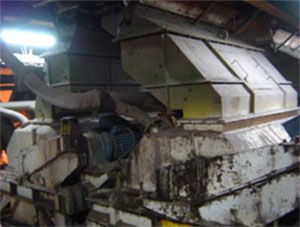
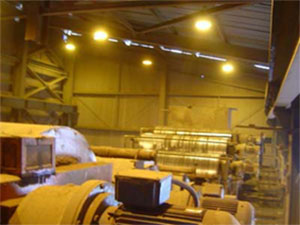
احیاء مستقیم
- میدرکس
در این روش که شبیه کوره بلند می باشد پلت و گندله از بالای کوره وارد و گاز های H2 & CO از پایین کوره دمیده می شود و به دمای حدود 750 در سانتی گراد رسانده می شود جریان گاز و پلیت در این روش به صورت مداوم است و آهن اسفنجی تولید شده در قسمت پایین کوره شروع به سرد شدن می کند.از مزایای این روش به راه اندازی سریع و سرعت بالی بازدهی و مصرف سوخت پایین اشاره کرد.
- اچ وای ال
در این روش از چهارکوره به صورت همزمان استفاده می گردد روش کار بدین گونه است که 1- اولین کوره در حال تخلیه و بارگیری می باشد، کوره دوم به صورت پیشگرم فعال است 3- کوره سوم به صورت احیاء کردن است 4 – کوره چهارم درحال سرد شدن می باشد.
کک سازی
احیاء:
با جداسازی اکسیژن از اکسید آهن و آزاد شدن آهن، فرآیند احیاء سنگ آهن انجام می پذیرد. تمام واکنش های کوره بلند در درجه حرارت های زیاد نتیجه سوختن کک می باشد از ذغال سنگ برای تهیه کک و عمل احیاء و ذوب در کوره بلند استفاده می شود البته به مقدار بسیار کم از گاز طبیعی و مازوت نیز استفاده می گردد.
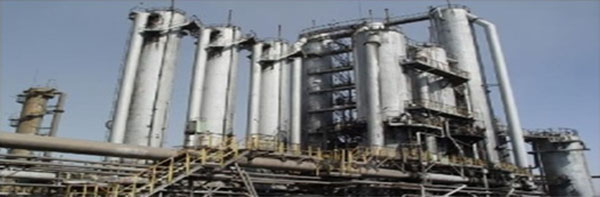
کک علاوه بر تامین انرژی حراریی لازم در کوره بلند عمل احیاء اکسیدهای آهن موجود در سنگ آهن را نیز انجام می دهد.ارزش حرارتی کک باید حداکثر و رطوبت آن حداقل باشد.
قسمت های مختلف کک سازی و مواد شیمیایی
1. بخش ذغال
آماده سازی و ذخیره ذغال سنگ برای شارژ در سلول های کک سازی در بخش ذغال انجام می شود. ذغال سنگ ها پس از ذخیره سازی در سیلوها در آسیاب های چکشی خرد و به وسیله نوار نقاله به سمت باطری های بخش کک وارد مخلوط کن می شوند.
2. بخش کک
ذغال سنگ های آماده شده توسط واگن شارژ در سلول های کک سازی شارژ شده و در مدت مشخصی کک سازی می شوند.این فرآیند طی 5 مرحله انجام می گردد.
سلول هایی که در آنها گاز کک تصفیه شده با هوا می سوزد سلول گرمایی و سلول هایی که در آنها ذغال شارژ می شود، سلول کک نامیده می شود. کک گداخته شده پس از خنک سازی شده توسط نوار نقاله به بخش دانه بندی ارسال و سرند می شوند.
- دانه های کک کوچکتر از 25 میلیمتر به عنوان سوخت در آگلومراسیون
- کک های 80-25 میلیمتر برای کوره بلند
- کک های با دانه بندی بزرگتر از 80میلیمتر مجدد به بخش دانه بندی و سرند وارد می شوند و بخشی از آن در کوره ریخته گری کوپل ریخته می شود.
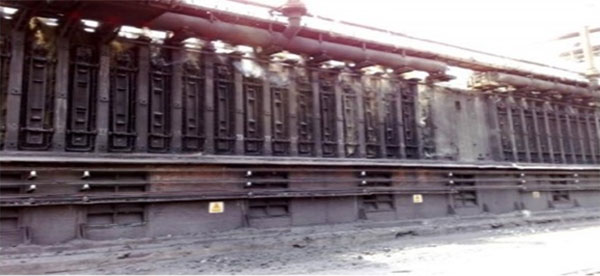
روش خاموش کردن کک
1 - روش تر:
برای خاموش کردن کک از روش تر با پاشیدن آب سرد روی کک های داغ استفاده می شود.
2 – روش خشک:
در روش خشک از گاز بی اثر ازت استفاده نمی گردد زمانیکه مقدار رطویت کک کم می شود استحکام آنرا افزایش می دهیم، البته از انرژی گرمایی گاز دمیده شده به کک نیز می توان با تکنولوژی و تجهیزات پیشرفته نیز استفاده نمود.
پالایش و باز یابی مواد شیمیایی کک:
گاز کک پس از خروج از سلول کک سازی به طرف بخش بازیابی مواد شیمیایی فرستاده می شود. در این بخش با روش های مختلف شیمیایی گاز کک جدا می شود.
اهمیت گازکک
- ارزش حرارتی خوب در حدود 4000 کیلو کالری بر متر مربع
- ارزش شیمیایی گاز کک به صورت خام یا تصفیه نشده دارای مواد شیمیایی بارزشی مانند (بخار آب، بخار قطران، آمونیاک، نفتالین و غیره) می باشد.
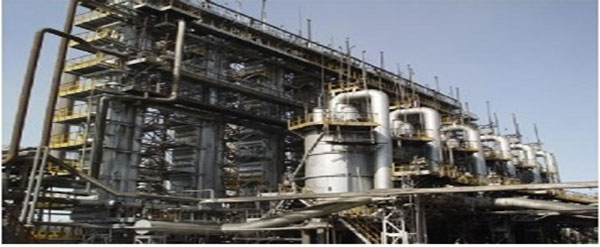
تصفیه گاز کک خام
گاز کک خام تولید شده از فرآیند کک سازی ابتدا به وسیله پاشیدن آب آمونیاک سرد می شود و قطران و و نفتالین همراه با ذرات کک از آن جدا می شود.پس از آن با دمیدن گاز با دمای پایین و عبور آن از سپراتورها مواد سنگین باقی مانده قطران و آب آمونیاکی نیز جدا می شود.گاز کک در مرحله بعدی از برج های خنک کننده گذشته و دمای آن کاهش محسوسی می یابد.سپس با عبور از بخار آب وارد و با عبور از سطح اسید سولفوریک، سولفات آمونیوم ته نشین می گردد.گاز خروجی از قسمت اسید سولفوریک وارد شبگه گاز کارخانه می شود از آن برای گرم کردن سلول های کک سازی یا تولید بخار در نیروگاه ها یا کوره پیش گرم نورد یا ماشین های پخت آلگومراسیون می شود.
ترکیب شیمیایی کک
مهمترین دلیل وجود رطوبت در کک پس از خاموش کردن آن به حفره های کک است. هنگام انبار کردن در فضای آزاد کک بسرعت رطوبت خود را از دست می دهد.
آهک پزی
بیشترین کاربرد سنگ آهک در صنایع فولاد سازی و آهن مصرف می شود،آهک به عنوان روانساز و گذار آور برای افزایش سیالیت سرباره و کاهش نقطه ذوب سیلیس می بایست به کوره افزوده شود.اهک را می توان از طریق تکلیس از سنگ اهک بدست آورد.
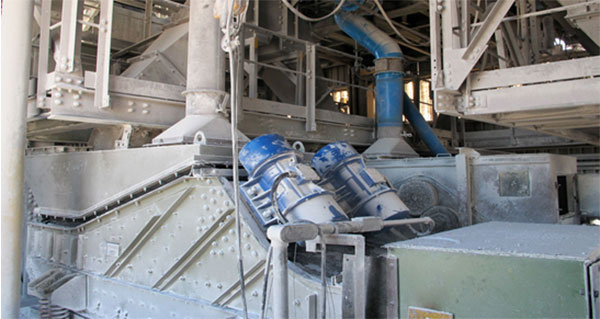
به دلیل استحکام پایین، آهک را مستقیما به کوره اضافه نمی کنند و برای استفاده از آهک ابتدا آنرا به واحد آگلومراسیون فرستاده و به همراه مواد دیگر به صورت آلگومره استفاده می شود.
آگلومراسیون
نرمه های آهن را برای شارژ کوره های بلند و یا احیا به یکدیگر می چسبانند. به اینگونه روش ها آگلومراسیون می گویند.
اهداف آگلومراسیون:
- استفاده از نرمه های سنگ آهن
- افزایش کیفیت بار وارد شده به کوره های بلند
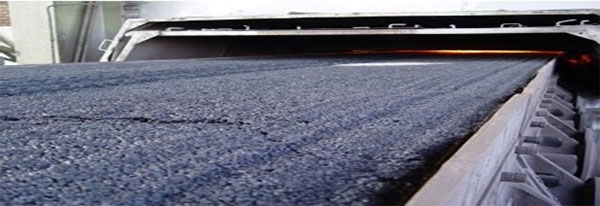
روش های آگلومراسیون
- پلت سازی یا گندله سازی
- بریکت سازی
- کلوخه سازی یا سینتر سازی
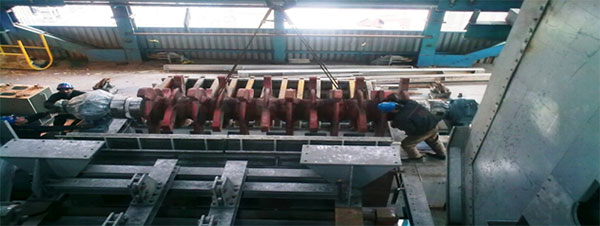
قسمت های آگلومراسیون
- انبار مواد خام
- آماده کردن مواد خام ( آسیاب چکشی، آسیاب چهار غلطکی، نقاله های ثابت و متحرک، سیستم توزین، موتور و گیربکس مخلوط کن مواد
- کارگاه پخت و تصفیه هوا
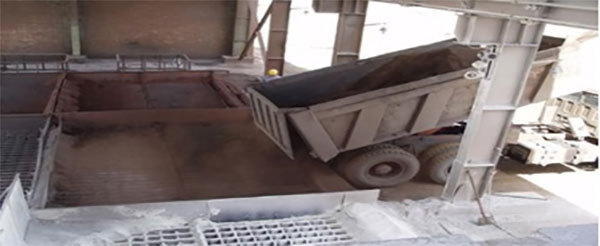
قسمت تلغیظ
لجن ها ابتدا وارد مخزن اصلی شده و سپس توسط پمپ ها وارد ردیف های هیدروسیکلون شده،در هر هیدروسیکلون، در اثر حرکت گریز از مرکز لجن مقداری آب از آن جدا می شود.
کارگاه پخت:
معمولا از یک ساختمان هفت طبقه که شامل تجهیزات زیر است تشکیل شده است:
- در بالاترین طبقه بونکر های مواد آماده قرار می گیرد.
- بونکرهای پاستیل که برگشتی آگلومتره در آن ذخیره می شود.
- مخلوط کن دوم که برای مخلوط کردن مواد خام قبل از ورود به ماشین پخت قرار داردکه همزمان با چرخش مخلوط کن آب روی مواد پاشیده می شود.
- ماشین های پخت
- بستر خنک کننده ( لنت سرد) که کلوخه های پخته شده برای خنک شدن و بعد از گذشتن از خرد کن روی آن ریخته می شود و از زیر هوای سرد به آن دمیده می شود.
- سرندهای خود تراز که در پایان بخش خنک کن قرار دارد.
- نوار نقاله زنجیری وظیفه جمع آوری لجن موجود در آب که بر اثر گرد و غبار زیر سیکلون ها به وسیله مکش هوا در وان آب ریخته را دارد.
نمونه موتور فن کوره پخت گندله سازی ذوب آهن
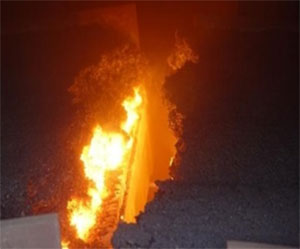
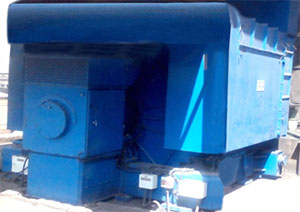
کوره بلند
وظیفه کوره بلند احیاء سنگ آهن و تولید چدن مذاب است. احیاء سنگ آهن از طریق حذف اکسیژن به وسیله گاز مونواکسید کربن که از سوختن کک بدست می آید انجام می گیرد.
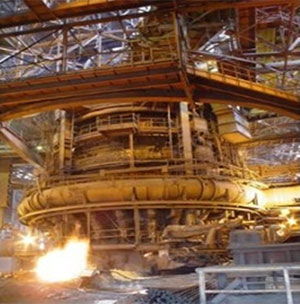
قسمت های کوره بلند:
- بونکر های مواد خام
- تجهیزات بارگیری کوره بلند
- بدنه کوره بلند
- کارگاه چدن
- پیش گرمکن های هوا
- تجهیزات غبار گیر و تصفیه گاز
- کارگاه ریخته گری چدن
- کارگاه دانه بندی سرباره کوره بلند
بدنه کوره بلند:
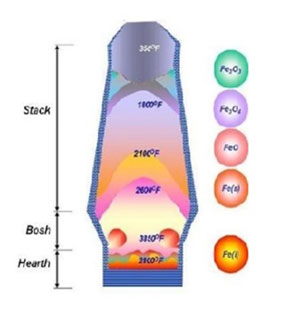
شمایی از کوره بلند
پوسته کوره بلند:
جنس پوسته کوره از ورقه های فولادی تهیه می گردد که داخل آنرا آجرهای نسوز قرار می دهند وظیفه اصلی بدنه محافظت و نگهداری آجرنسوزها در برابر با فشار مواد شارژ شده و همچنین نگهداری خنک کننده های آبی و جلوگیری از خروج گازهای داخل کوره به خارج کوره است.
ساختمان بوته کوره بلند
- لایه داخلی
- لایه خارجی
سرد کردن کوره بلند
- خنک کردن پوسته خارجی کوره بوسیله ریزش آب روی آن
- خنک کردن به وسیله خنک کننده های مخصوص
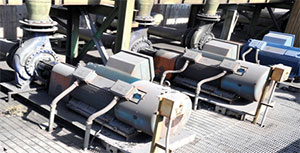
پمپ های سیستم آبگرد کوره های قوس الکتریکی ( پمپ ها تیپ HPEB 30X55، تولیدی شرکت چرپلی ایتالیا می باشند)
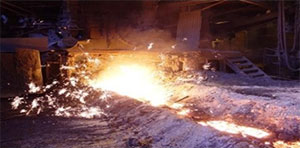
ساختمان دستگاه دمنده هوا به کوره بلند:
هوای گرم شده با درجه حرارت 1150 تا 1100 درجه سانتی گراد از هوا سانتی گراد از هوا گرم کن ها از طریق لوله اصلی هوای گرم وارد لوله کمربندی شده و از آنجا بوسیله سیستم دمنده هوا و فرم ها وارد کوره بلند می شود. برای جلوگیری از سوخته شدن لوله های گرم و انتقال حرارت به خارج، داخل آنها با آجرهای نسوز پوشانده شده است تعدادشیپورک ها یا فرم ها به قطر بوته کوره بلند بستگی دارد شیپورک ها را از مس می سازند و بوسیله گردش آب در آنها از سوختن آنها جلوگیری می کنند.
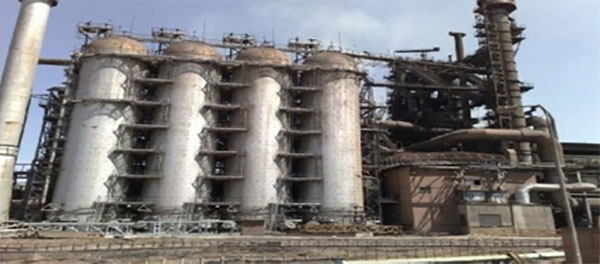
سیستم شارژ مواد به داخل کوره بلند:
هربار که زنگ بزرگ باز می شود مواد به داخل کوره ریخته می شوند به این مواد یک شارژ می گویند.
تهیه هوا برای کوره بلند:
حجم هوای مصرف کوره بلند زیاد است و اگر وزن ورودی به کوره بلند را حساب کنیم از وزن تمام مواد خام ورودی به کوره بیشتر می شود. هوای مصرفی در کوره بلند بوسیله پیش گرمکن ها تولید می شود تا در مصرف کک صرفه جویی گردد و سرعت تولید را افزایش می دهد. (گرماگیری کوپر)
تهیه بخار کوره بلند
مصرف بخار در کارگاه کوره بلند معمولا 150-50 کیلوگرم به ازای هر تن چدن است.
موارد استفاده از بخار در کوره بلند
- بین زنگ کوچک و بزرگ
- زیر زنگ بزرگ هنگام توقف کوره
- همراه هوای دمش برای سرد کردن کوره
(نمونه یونیت هیدرولیک با فشار کاری 200bar شامل مخزن 1600lit، پمپ کارتریج دوبل ولجان VELJAN، شیرآلات کنترل برای فشار شکن برقی بلوکی سایز یک و یک چهارم برای عبوردهی روغن با دبی حدود 600lit/min، الکتروموتور زیمنس، خنک کن هوایی، فیلتر خط برگشت، شیرهای یکطرفه بلوکی، پرشر سوئیچ Duplomatic و شیر …decompression)
تصفیه گاز کوره بلند
گاز خارج شده از کوره بلند به عنوان سوخت مورد استفاده قرار می گیرد. در اثر سوختن یک تن کک کوره بلند 5000 متر مکعب گاز حاصل می شودکه ارزش حرارتی آن 900 کیلو کالری بر متر مکعب می باشد. گازهای دهانه به عنوان سوخت در هوای گرم کن های کوره بلند، کوره های کک سازی، چاه های گرم کننده و در تاسیسات دیگ های بخار مصرف می شود.
ماشین های ریخته گری چدن
ماشین ریخته گری چدن برای ریختن شمش های کوچکی از آهن که برایحمل و نقل و انبار کردن راحت تر است به کار می رود این ماشین در جنب کوره بلند و در محوطه مخصوص ریخته گری کار گذاشته شده است.
بخش ریخته گری چدن محوطه سرپوشیده ای است که در داخل آن ریل راه آهن کشیده شده و واگنهای حاصل پاتیل های آهن از طریق آنها به ماشین ریخته گری رسانده می شوند.
ماشین ریخته گری از یک نوار نقاله مورب ( شیب دار) که قالب های مخصوصی برای ریختن آهن مذاب بر روی این نقاله قرار داده شده است.
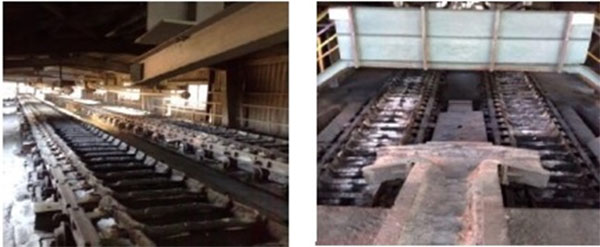
آماده کردن کوره بلند برای روشن کردن
برای محافظت بلوک های بوته از ضربه های حرارتی هتنگام احتراق کک، کف بوته را با لایه هایی از سرباره می پوشانند سپس کمی بالاتر از شیپورک ها، چوب و تراورس بارگیری می کنند.مواد خام را از طیق دستگاه شارژ کننده وارد کوره می کنند در اثر سوختن چوب ها ابتدای روشن شدن، شرلیط مساعدی برای فرو کش کردن مواد خام ایجاد می گرددبه علاوه مواد به طور گداخته وارد بوته می شود بنابراین موجب سرد شدن کوره نمی شود. اگر روشن کردن بوته بدون ریختن چوب در بئته انجام شود کک خیلی آهسته گرم می شود و خوب نمی سوزد این جریان منجر به متوقف شدن حرکت مواد و تشکیل توده غیر قابل ذوب از کک سرد و سرباره چسبیده در کف بوته می گردد.
عملیات روی سرباره کوره بلند
سرباره کوره بلند را به عنوان ماده خام برای تولید مصالح ساختمانی از جمله سیمان و سیمان سرباره، آجرها و بلوک های نسوز بکار می برند.
قبل از استفاده از سرباره به عنوان ماده خام بایستی آن را دانه بندی کرد برای اینکار سرباره را داخل ناودانی میریزند و از زیر ناوان آنرا سرد و خنک می کنند و تبدیل به دانه ریز می شود.
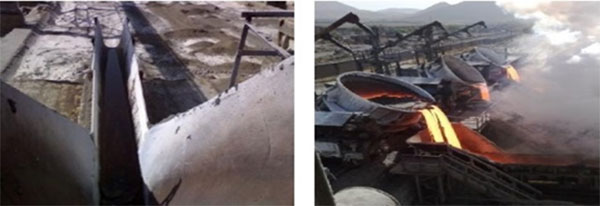
فولاد سازی
برای تولید فولا د کارگاه های میکسر، کنوکتور، کوره پاتیلی (L.F) ریخته گری مداوم، آماده سازی و تعمیر پاتیل، آهن قراضه، سرباره، کارگاه آماده سازی و ارسال شمش می باشد.
میکسر
وظیفه اصلی میکسر ذخیره و تامین چدن مذاب با دما و ترکیب شیمیایی یکنواخت برای کارگاه کنوکتور می باشد.از مزایای میکسر جلوگیری از افت درجه حرارت مذاب و هماهنگ نمودن روند کار کوره بلند و کنوکتور و جلوگیری از توقف پاتیل های حامل چدن می باشد.
روش تولید فولاد
برای تبدیل چدن به فولاد باید مقداری از ناخالصی های آن (کربن، سیلیسیم، منگنز، گوگرد، فسفر و ...) حذف شود و خارج کردن این عناصر به جز گوگرد توسط فرایند اکسیداسیون صورت می گیرد.
روش های تولید
- تولید توسط دمش هوا
- تولید توسط دمش اکسیژن
- تولید توسط کوره زیمنس مارتین
- تولید توسط انرژی الکتریکی
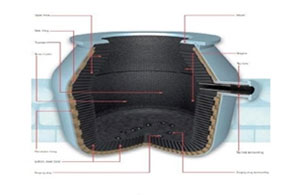
مراحل شارژ کنورتور
مراحل کار کنورتور بدین ترتیب است که پس از تخلیه ذوب قبلی کنورتور زا سمت دیگر بارگیری چرخانده تا آستر دهانه کنورتور به خوبی مشاهده گردد.پس از بازرسی آستر نسوز و تمیز کردن دهانه کنورتور در صورتی که مشکل خاصی در نسوز کنورتور مشاهده نگردد امکان عملیات فولاد سازی می باشد، آهن قراضه به وسیله ماشین شارژ قراه به داخل کنورتور شارژ می شود.در این مرحله باید دقت نمود به منظور کاهش صدمات مکانیکی بر آستر نسوز ارتفاع سقوط آهن قراضه حداقل باشد.
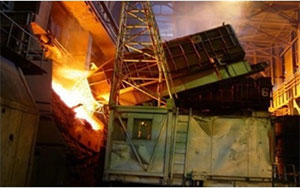
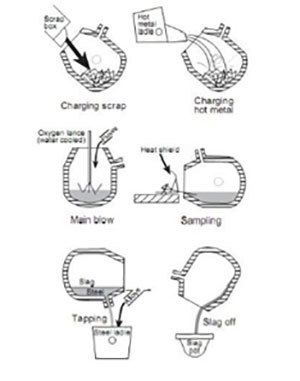
وظایف آهن قراضه
از آهن قراضه در کنورتور و به منظور متعادل کردن درجه حرارت مذاب استفاده می شود و مقدار آن در مواد اولیه به درجه حرارت و ترکیب شیمیایی چدن مذاب مصرفی و مقاومت نسوز کنورتور بستگی دارد.
مزایای روش LD:
- ساختمان ساده کنورتور
- امکان حذف کربن تا حدود مورد نظر
- مقداربسیار کم ازت در فولاد حاصله به علت دمش اکسیژن به جای هوا
- ظرفیت بالای کنورتور
- مقدار بیشتری آهن قراضه جهت استفاده از حرارت اضافی که در کنوکتور ایجاد می شود می توان استفاده نمود.
معایب روش LD
- خارج شدن مقدار زیادی اکسیدآهن همراه گازهای خروجی و سرباره
- کاهش قابل ملاحظه وزن فلز مذاب
اکسیژن:
اکسیژنی که در روش LD مورد استفاده قرار می گیرد به اکسیژن صنعتی موسوم است و برای بدست آوردن اکسیژن خالص از مراحل زیراستفاده می شود:
- مرحله تمیز کردن هوا از هرگونه ناخالصی مثل ذرات گرد و غبار، گاز کربنبک CO2 و رطوبت.
- فشرده نمودن هوا تا فشاری حدود kg/cm² 200.
- سرد کردن هوا توسط سرمایی که از تبخیر ازت حاصل می شود.
- انبساط هوای فشرده برای رسیدن به زیر درجه حرارتی که هوا مایع می شود.
- جدا کردن ازت توسط تبخیر جزیی.
پاتیل:
در پاتیل ها تخلیه فولاد به دو روش استوپری و دریچه کشویی انجام می گیرد.
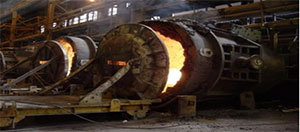
قسمت های اصلی ریخته گری مداوم:
1) پاتیل میانی ( تاندیش)
به منظور جلوگیری از مسدود شدن مجرای خروجی می بایست قبل از ریخته شدن مذاب در تادندیش آن را پیش گرم کنیم.
پاتیل میانی ریخته گری مداوم به عنوان واسطه ای بین پاتیل و کریستالیزاتور بکار می رود و وظیفه تنظیم سرعت را به عهده دارد.
پاتیل میانی وظیفه ذخیره ذوب و جلوگیری از ورود ناخالصی به صورت مستقیم به قالب را برعهده دارد.
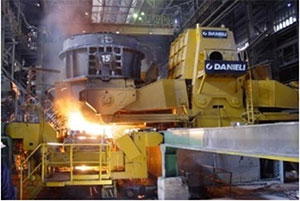
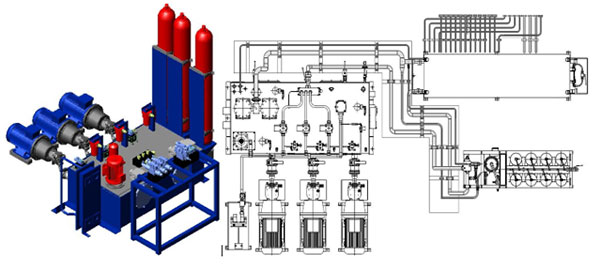
یونیت هیدرولیک کوره پاتیلی
درمورد تجهیزات این کوره ها می توان به پمپ های هیدرولیک، کمپرسور هوا، سیستم پنوماتیک شیلنگ هوادهی، رولبرینگ و غلتک ها انواع کابل و سیم های بکسل و زنجیری، موتور گیربکس، ترانسفورماتور و... نام برد.
2) قالب ( کریستالیزاتور)
مهمترین بخش ریخته گری مداوم قالب آن است. وظیفه قالب ایجاد یک پوسته جامد از فولاد مذاب است که مرکزاین پوسته فولاد مذاب است. این پوسته می بایست توانایی آن را داشته باشد که پس از خروج شمش قالب در برابر فشار فلز مذاب داخلی شمش مقاومت کند.
روغن کریستالیزاتور
روغن کاری کریستالیزاتورعلاوه براینکه ازاکسید شدن سطح فولاد درون آن جلوگیری می کند مانع چسبیدن مذاب فولاد به دیواره کریستالیراتور می شود.
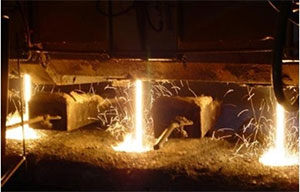
سرد کننده ثانویه:
در زمانیکه شمش از قالب ( کریستالیزاتور) خارج می گردد فقط قشر خارجی آن سرد شده است در صورتیکه درون آن هنوز مذاب است. در بخش سرد کننده ثانویه توسط پاشش آب انجماد شمش کامل می گردد. تنظیم میزان سرد کنندگی چه در مقطع طولی و چه در مقطع عرضی بسیار مهم است در صورتیکه شمش سریع سرد شود احتمال ترک وجود دارد همچنین آهسته سرد کردن نیز باعث می شود مرکز شمش به صورت مذاب باقی بماند.
کشیدن شمش:
کشیدن شمش از قسمت سردکننده ثانویه و کریستالیراتور به عهده دستگاه کشاننده است این دستگاه از چهار غلطک که دردو طرف شمش واقع شده است تشکیل می گردد.شمش قبل از رسیدن به دستگاه کشانده باید کاملا سرد و منجمد شده باشد.در غیر اینصورت ترک هایی درداخل شمش به وجود می آید. تنظیم سرعت حرکت شمش توسط غلطک های کشاننده انجام می شود که این سرعت باید متناسب با جریان ذوب درون قالب باشد این فرآیند توسط چشمه رادیواکتیو که درون قالب تعبیه شده است به موتور کشاننده و متناسب با سطح ذوب در کریستالیاتور فرمان می دهد و سرعت حرکت شمش کنترل می گردد.

کارگاه ریخته گری مداوم
بعضی از کارگاه های فرآیند ریخته گری از تکنولوژی روسی و دانیلی استفاده می شود. در این ایستگاه ابتدا فولاد در پاتیل میانی و سپس به درون کریستالیزاتور ریخته می شود در اثر سرد شدن دیواره قالب توسط پاشش آب مذاب منجمد می گردد پس از خارج شدن پوسته جامد به همراه مذاب از کریستالیزاتور در منطقه سرد کننده به وسیله پاشش مستقیم آب، داخل و مغز شمش نیز جامد می گردد.
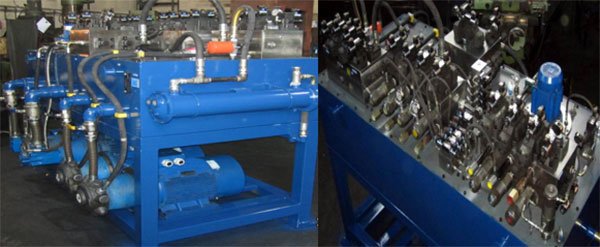
( نمونه یونیت هیدرولیک با حجم مخزن 1600lit و فشار کاری250bar شامل انواع پمپ دنده ای روکت دوبل، پمپ تیغه ای دوبل، پمپ های پیستونی، شش مجموعه الکتروموتور، چهل و پنج مجموعه انواع شیرهای کنترل جهت، دبی و فشار هایدمک، خنک کن آبی، هیتر، پرشر سوئیچ، لول سوئیچ، فیلتر خط برگشت...)
کارگاه شمش
معمولا شمشی که در قسمت ریخته گری تولید می شود، دارای عیوب می باشد( ترک، موج، ترک های درونی، حفره های داخلی و...) برای از بین بردن عیوب سطحی روشهای مختلفی وجود دارد که معمولا از روش بکارگیری شعله و سوزاندن رفع و نقص سطحی است
نورد
یکی از روش های مهم شکل دهی، نورد است که در این بخش از حجم شمش یا فلزی که شکل داده می شود چیزی کم نمی شود. به عبارت دیگر براده برداری از فلز انجام نمی گیرد نورد بدین صورت انجام می گیرد که شمش مورد نظر پس از گذشتن از بین غلطک ها که در جهت عکس یکدیگر حرکت می کنند به شکل مطلوب تبدیل خواهد شد.
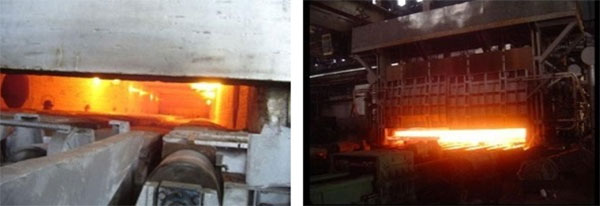
نمونه ایی از تجهیزات بکار رفته در دپارتمانهای مختلف تولید فولاد
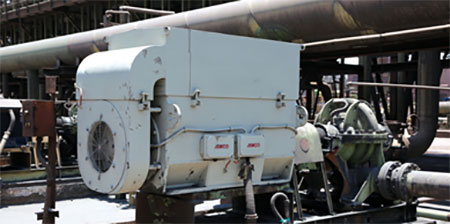
بومی سازی موتور پمپ های آبرسانی واحد فولاد سازی ( فولاد مبارکه)
سیستم جابجایی بلوک های هیدرولیک خط ورق
کمپرسور چیلرهای واحد تصفیه آب و توزیع سیالات و Mechanical Seal
کنترل سرو ولوهای پینچ رول واحد ریخته گری
سیستم هیدرولیک واحد بسته بندی در ناحیه نورد سرد
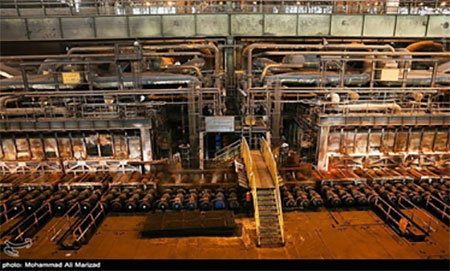
لیست قیمت مهندسی فرآیند تولید فولاد
با عرض پوزش کلیه قیمت ها در حال بروزرسانی می باشد، لطفا جهت استعلام قیمت خرید با واحد فروش تماس حاصل نمایید.