مشخصات فنی مهندسی فرآیند تولید لاستیک خودرو
لاستیک (Tire) برای محافظت از چرخ و عملکرد بهتر خودرو در زمانی که چرخ ها با زمین در تماس هستند تولید گردیده اند بر روی هر تایر آج هایی وجود دارند که این امکانر ا می دهند که کشش بیشتری در سطح تایر به وجود بیاید و همچنین از ساییدگی و خرابی زود هنگام تایر جلو گیری نماید.
اجزای کلی تایر

انواع تایر:
تایرهای بایاس
در این نوع تایرها همانطور که در شکل زیرمشاهده می شود امتداد نخ های لایه با خط مرکزی تایرزاویه مورب می سازد و قرار گیری لایه ها روی یکدیگر به صورت ضربدری می باشد. جنس نخ لایه ها از نایلون است و دربدنه تایر بجز در ناحیه طوقه ها از سیم فولادی استفاده نمی شود(تصویر سمت راست).
تایرهای ردیال
در تایرهای ردیال که در شکل نیز مشخص می باشد امتداد نخ های لایه با خط مرکزی تایر زاویه 90 درجه می سازد به عبارت دیگر امتداد نخ ها در جهت شعاعی می باشد. جنس و مواد بکار رفته در نخ ها معمولا از پلی استر یا ریون است. در این تایر ها به منظور پایداری حرکتی از کمربند یا بلت در جهت حرکتی لایه های به عرض عاج و زاویه مورب نسبت به خط مرکزی تایر استفاده می شود.جنس این کمر بندها از جنس نخ یا سیم فولادی است (تصویر سمت چپ).
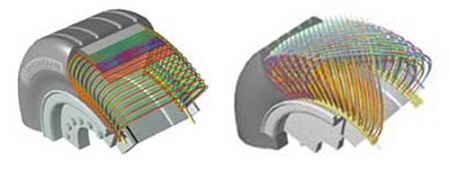
خط تولید تایر:
در صورتی که کمربند نخی باشد تایر را رادیال نخی و در صورتی که سیمی باشد تایر را رادیال سیمی ( استیل بلت) می سازند.
تایرهای رادیال به دلیل مزایای ویژه ایی که نسبت به تایرهای بایاس دارند در سالهای اخیر مورد توجه قرار گرفته اند. هرچند که تولید این تایرها بر اساس نوع طبقه بندی آن (باری سبک و سنگین) و همچنین نوع فناوری مورد استفاده ( بایاس و رادیال ) در مراحلی از تولید با یکدیگر تفاوت هایی دارند ، اما به صورت کلی می توان تولید آن را در چهار مرحله خلاصه کرد که جریان تولید را می توان در شکل زیر مشاهده نمود.
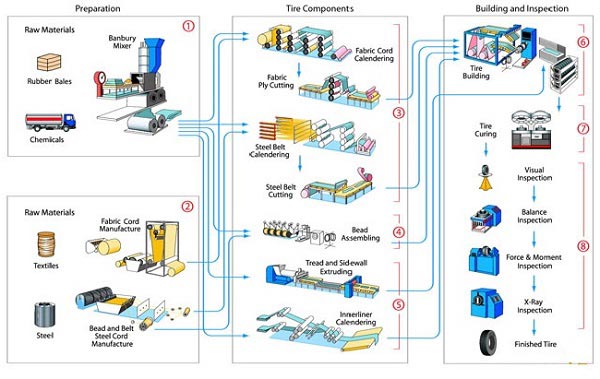
مرحله اول: فرایند اختلاط مواد و تهیه ترکیبات لاستیکی ( کامپاند)
در این بخش مواد اولیه با یکدیگردر ددستگاه مخلوط کن ( بنبوری ) مخلوط می گردند و انواع ترکیبات لاستیکی از جمله کائوچو(طبیعی و مصنوعی )دوده ، روغن ها و مواد شیمیایی بدست می آید.از ترکیبات لاستیکی در بخش های مختلف لاستیک استفاده می شود و از آنجاییکه هر تایرخواص فیزیکی و مکانیکی متفاوتی می باشد، لذا ضرورت دارد که ترکیبات متفاوتی از مواد لاستیکی تهیه گردد.

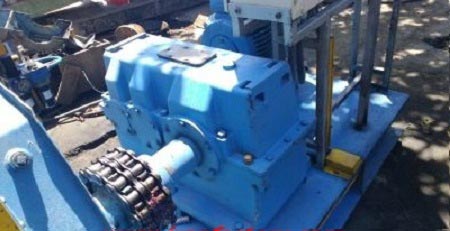
بنبوری
دستگاه اختلاط داخلی است که از سه قسمت تشکیل شده است
1) قسمت تغذیه
شامل قبف تغذیه برای دریافت مواد می باشد همچنین یک رام برای نگهداری مواد در داخل اطاقک اختلاط تشکیل یافته است . حرکت عمودی و باز و بسته شدن دریچه قیف تغذیه به وسیله فشار هوا صورت می گیرد.
2) قسمت اختلاط
از دو سیلندر به هم مرتبط که درون آن از دو مارپیچ حلزونی که روتور نامیده می شود تشکیل یافته است. این روتورها در کنار هم درون این سیلندرها قرار گرفته اندو درجهت عکس یکدیگر با سرعت های متفائت ، نسبت به یکدیگر در حال چرخش هستند روتورها توسط موتورهای با ولتاژ بالا کار می کنند.
3) قسمت موتور
برای اختلاط مواد در داخل محفظه اختلاط بنبوری ، موتوری قراردارد که روتور ها را به چرخش در می آورد.
آمیزه کاری
آمیزه کاری مرحله ای است که در آن با بدست آوردن بهترین فرمولاسیون برای ترکیب کردن چند نوع ماده مختلف با لاستیک انتخابی ، برای رسیدن به پارامتر هایی مانند خواص دلخواه، ولکانش بهتر و راحت تر، روش شکل دهی مناسب تر و رسیدن به قیمتی معقول تر، این مواد با لاستیک مخلوط شده و آمیزه لاستیکی آماده فرآیند می شود. پس باید گفت مسئول آمیزه کاری وظیفه مهمی بر عهده دارد.
در صنعت در اغلب روش ها ، نرم کردن (Masticating)، ترکیب و اختلاط مواد اولیه در لاستیک با استفاده از غلطک و یا مخلوط کن داخلی که به آن بنبوری ( Banbury Mixer ) که پرکاربرد ترین دستگاه است می گویند انجام می شود.
مرحله دوم: فرایند ساخت و آماده سازی اجزا تایر
ساخت و آماده سازی اجزای تشکیل دهنده تایر در بخش های مختلف صورت می پذیرد.
نمونه دستگاه سرشانه و هامپ
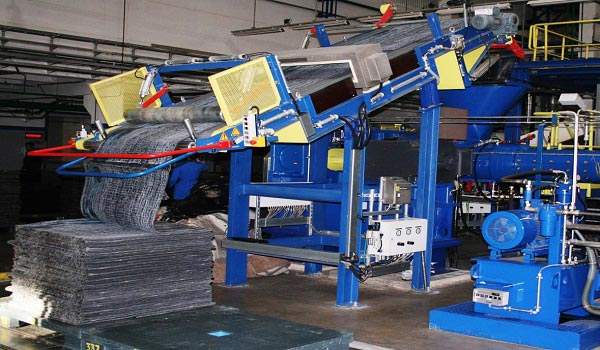
بخش اکسترودر: ساخت ترد، دیواره ها، نوارهای لاستیکی، سرشانه و هامپ
بخش کلندر:
ساخت لایه ها (جزء عمده بدنه یا منجید تایر) محصول کلندر فابریک یا الیاف نخ و یا سیم است که توسط این لاستیک پوشش داده شده است از کلندر برای تولید گام یا اسکوییچی ، انجام عملیات فربکشن یا اندود کردن و پوشش دادن استفاده می شود بیشترین کاربرد را کلندر های 4 رولی دارند.
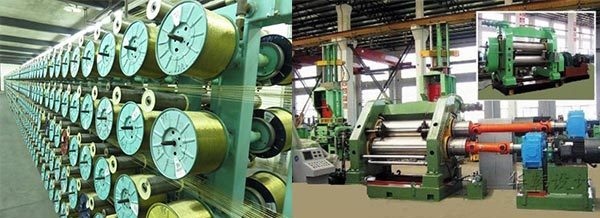
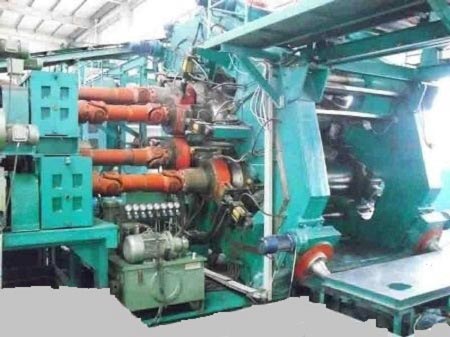
بخش بیدسازی:
ساخت بلت سیمی روی دستگاه استیلاستیک و ساخت بید یا طوقه
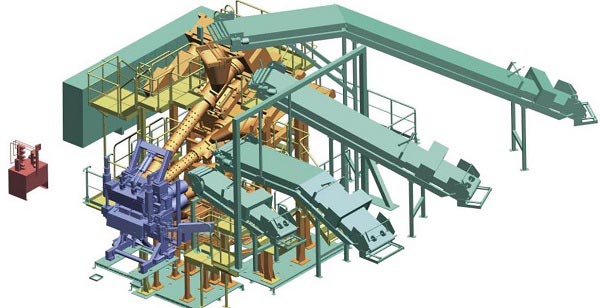
مرحله سوم:
بر خلاف تایرهای سبک از جمله بایاس که در یک مرحله ساخته می شود ساخت تایرهای رادیال سیمی سواری معمولا در دو مرحله انجام می گیرد. در اولین مرحله منجید تایر شامل لایه ها ، بید و دیواره ها آماده می شوند و در دومین مرحله بلت سیمی و ترد به آن اضافه می گردد. در تعدادی از کارخانه های تایر سازی و در تایرهای سنگین بایاس تعدادی از لایه ها را بر روی ماشین بندسازی روی هم قرار می دهند و پس از آماده شدن بند ها آنها را به ماشین تایر سازی انتقال می دهند. با مونتاژ بندها روی هم و اضافه کردن بید و ترد به آن در ماشن آلات تایر سازی تایر سنگین تولید می گردد.
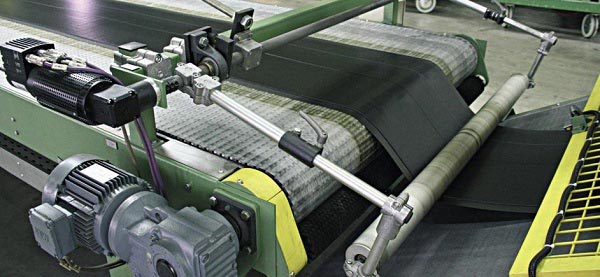
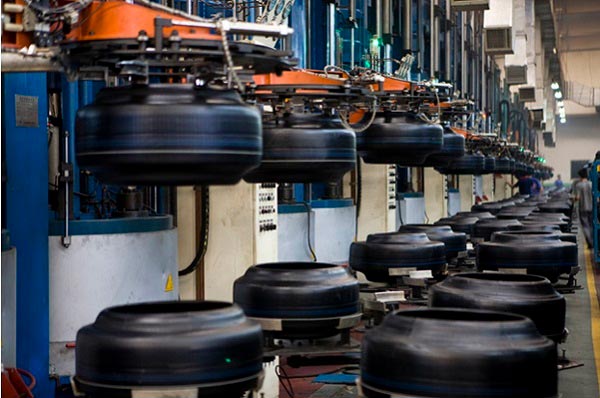
فرآیند پخت تایر:
آخرین مرحله تولید تایرکه تایر در آن شکل نهایی و خواص مکانیکی – دینامیکی خود را بدست می آورد، مرحله پخت یا ولکانیزاسیون می گویند ، لذا در این مرحله تایر با استفاده از عوامل پخت که هنگام مخلوط کردن ترکیبات لاستیکی به آن افزوده شده است بعد از قرار گرفتن در پرس پخت شکل نهایی به خود گرفته و با حرارت قالب و به دنبال ایجاد اتصالات عرضی در ترکیبات لاستیکی، خاصیت الاستیک و یا کشسان پیدا می کنند.
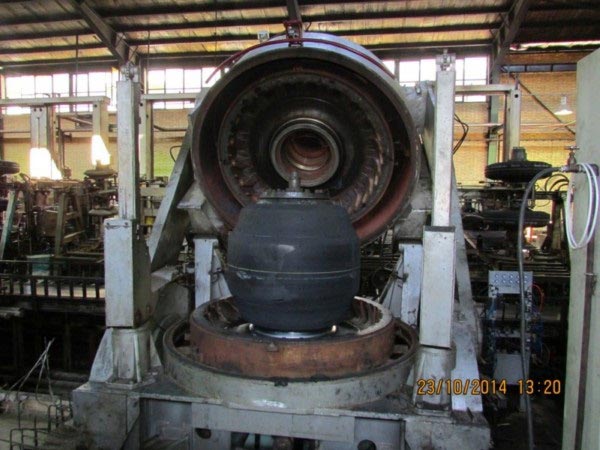
تولید تایر برخلاف اغلب فرایندهای تولیدی صنایع شیمیایی، فرآیندی غیرمداوم و یا به اصطلاح پیمانه ایی است . دراین فرایندبخشی از مواد نیمه ساخته درفرایندهای پیمانه ایی غیر مستمر ساخته می شوند و در فرایند های بعدی با هم تلفیق تا خوراک فرآیندهای مستمر و مداوم بعدی را فراهم سازند. از این مرحله به بعد دوباره مواد نیمه ساخته به دست آمده به بخش های جدا و منفک از هم تبدیل می گردند که طی یک سری فرایند های پرزحمت و کند از جمله تایر سازی و پخت ، به تایر تبدیل می شوند.
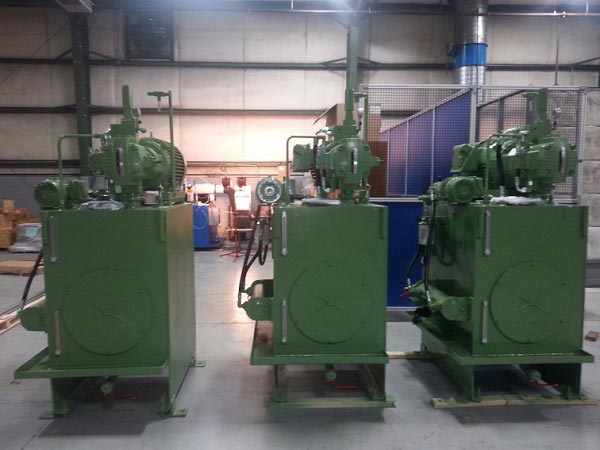
نمونه دستگاه هیدرولیک بخش پرس
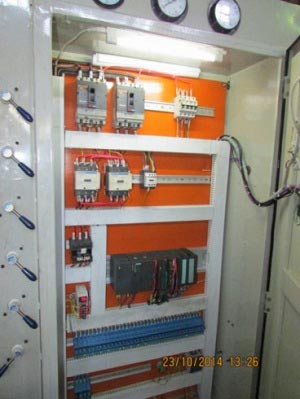
روش های ولکانش غیر پیوسته یا پیمانه ای (Batch Curing)
- اتو کلاو یا دیگ بخار (Autoclave or Steam Pan)
- پخت با گاز (Gas Curing)
- پخت با آون (Oven Curing)
- پخت با آب (Water Curing)
- پخت با پوشش سربی (Lead Curing)
- فرآیند پیچی (Peachey)
روش های ولکانش پیوسته (Continues Curing)
- لوله بخار تحت فشار(High-Pressure Steam Pipe)
- تونل هوای داغ (Hot Air Tunnel)
- ولکانش با اشعه (Radiation Vulcanization)
- پخت با نورUV
- پخت با حمام نمک (Liquid Curing Melt)
- پخت در بستر سیال
- پخت در غلتک چرخان (Steam Drum Cure)
- پخت با امواج مایکروویو(Microwave Curing)با میدان الکترو مغناطیسی (UHF)
شکل دهی
شکل دهی به معنی فرم دادن یا شکل گیری تدریجی یک آمیزه لاستیکی به همراه واکنش شبکه ای شدن آن می باشد. باید گفت ماشین آلات شکل دهی درلاستیک ها تقریباً مشابه ماشین آلات شکل دهی پلاستیک ها می باشد. انتخاب یک فرآیند شکل دهی باید با در نظر گرفتن پارامتر های فنی و اقتصادی و همچنین برای رسیدن به یک پخت کاملاً یکنواخت در محصول صورت پذیرد. در هنگام شکل دهی یا فرآیند پخت همزمان با شکل دهی صورت می پذیرد که به آن دسته ای (Batch) گویند و یا مانند تسمه نقاله یا شیلنگ یا روکش های کابل فرآیند پخت بعد از شکل دهی انجام می شود که به آن پیوسته (Continues) گویند.
شکل دهی به سه طریق انجام می شود:
- قالب گیری و تزریق
- قالب گیری فشاری
- قالب گیری انتقالی
- قالب گیری تزریقی
- اکستروژن
- اکستروژن با اعمال برش بالا در کلگی
- کلندرینگ
- کلندر دستگاهی است مخصوص شکل دهی و تولید ورق است ولی رل میل ها در اختلاف توزیعی ،per-shaping یا شکل دهی اولیه و یا برای mastication را برای هموژناسیون و غیره به کار می رود.
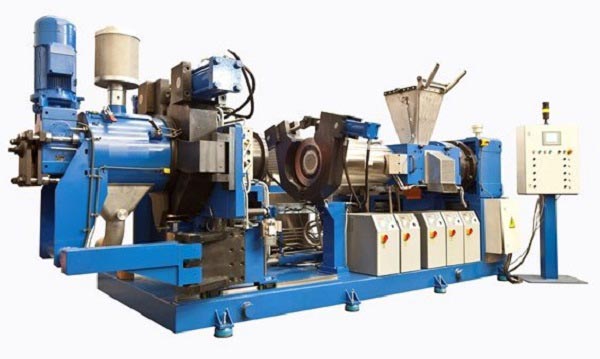
حرکت درون یک کلندر را می توان به سه قسمت تقسیم نمود:
- ناحیه تغذیه یا Feed Pass
- ناحیه اندازه گیری یا Metering Pass
- ناحیه شکل دهی یا Sheet Forming , Gauging or Finishing Pass
فرآیند بازرسی
در پایان لاستیک های تولیدی مطابق استاندارد های خاص مورد تست قرار می گیرند نواحی بیرونی و داخلی تایر تولید شده به صورت چشمی از نظر وجود عیوب ظاهری بازدید شده و در مراحل بعدی یا ماشین های آزمون ، مقادیر نابالانسی (سرب بری) و غیر یکنواختی اندازه گیری و مورد ارزیابی قرار گیرد و سپس با اشعه لیزر در دستگاه X- Ray عکسبرداری هایی از بخش های درونی تایر از نظر ورود حباب هوا و جدایی بین اجزای تایر صورت می گیرد.و تستهای دیگر از جمله تست کنترل فرمان و تست مصرف سوخت نیز انجام می شود.
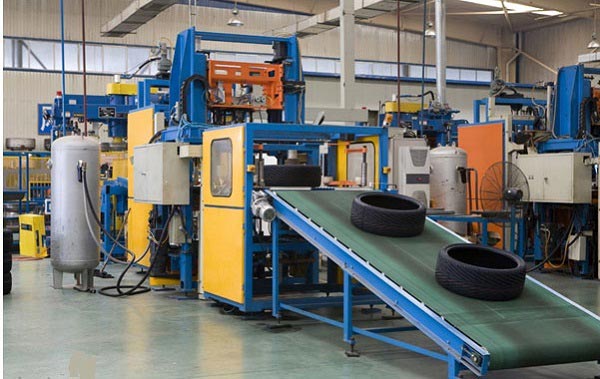
انواع تکنولوژی روکش تایر
در صنعت روکش تایر جهان متناسب با میزان سرمایه گذاری ، فرهنگ مصرفی جامعه ، شرایط مصرف تایر، وضعیت جاده ها و نوع منجیدهای قابل روکش، تکنیک های متفاوتی برای روکش تایر های مستعمل به کار گرفته می شود و به طور کلی دو نوع تکنولوژی گرو و سرد در صنعت روکش، شناخته می شود.
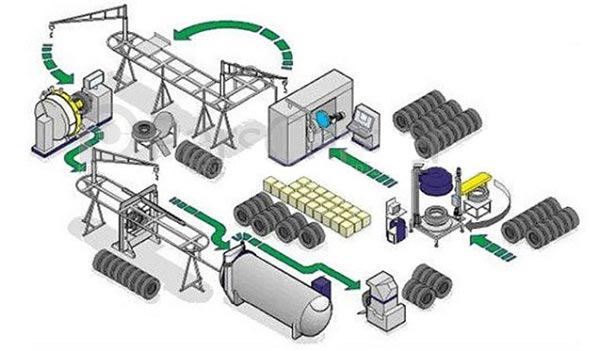
بازرسی منجید
برای شروع فرآیند اولین کار بازدید و بازرسی منجیدهای قابل روکش و غیر قابل روکش مطابق روش و دستورالعمل علی تعیین شده جدا و از هم تفکیک می شوند.
بافتینگ
در این مرحله ترد (Tread) سوخته از روی منجید، تراش داده می شود تا سطح منجید آمادگی پذیرش ترد جدید را داشته باشد. با توجه به نحوه ترد گذاری (سرد یا گرم ) نوع تراش منجدها متفاوت می باشد.
باف دستی و تعمیرات تایر
در این بخش کلیه قسمت ها که بصورت بریدگی و نخ زدگی پس از تراش روی منجید باقی مانده، توسط ابزار مخصوص پاک سازی و در صورت لزوم در مناطقی که روی منجید دچار ضعف یا سوراخ شده کار تعمیراتی و مقاوم سازی بوسیله وصله انجام می گیرد.
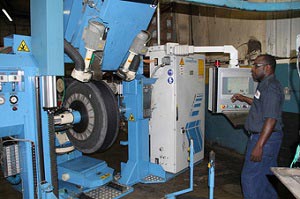
سمنت زنی
دراین بخش پس از اتمام کار تراش سطح منجید با یک لایه نازک که اصطلاحا به آن چسب می گوییم آغشته می شود . این کار توسط اسپری انجام می گردد
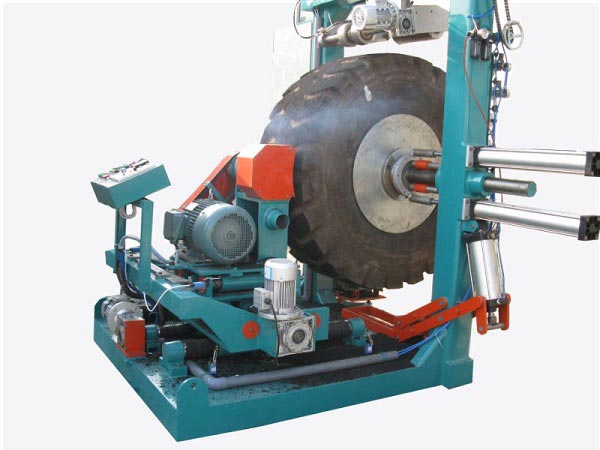
پر کن
در این واحد کلیه حفره ها ی ایجاد شده روی سطح منجید که در واحد باف دستی ایجاد شده و در کلیه نواحی نخ زده توسط مواد خاص ( کوشین) پوشش داده شده و یک سطح تقریبا یکنواخت برای ترد گذاری آماده می شود. در ضمن در این مرحله منجیدها مجددا توسط بازدید چشمی مورد تجزیه و تحلیل قرار می گیرد تا قبل از ترد گذاری در صورت وجود مشکل تایر اصلاح گردد.
ساخت
از این مرحله به بعد پروسه ی کاری روکش سرد و گرم با یکدیگر متفاوت می باشد که به شرح زیر توضیح داده می شود:
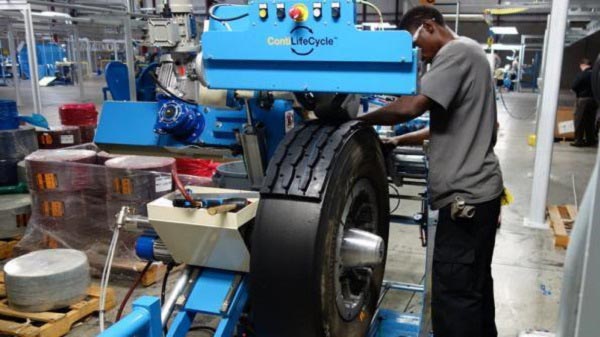
روکش سرد
در این بخش بعد از تراش و صیقل سطح منجید ، ترد مورد نظر که قبلا پخته و به صورت رول آماده شده برش خورده و پشت آن کوشین کشیده می شود. پس از آماده شدن منجید برای ساخت ، روی دستگاه بیلدر گذاشته شده و ترد بصورت دستی و بصورت یکنواخت روی آن کشیده می شود
روکش گرم
در این واحد منجید ها روی رینگ و دستگاه اکسترودر قرار گرفته و پس از تیوپلس شدن به روش Orbe Tread سطح منجید بصورت اتوماتیک ترد گذاری می گردد . که برای ساخت هر سایز تایر برنامه مخصوص آن سایز استفاده می گردد.
تفاوت روکش گرم سرد
در فرایند روکش گرم ، کامپاند ( مواد اولیه لاستیک ) بصورت نوار قرقره ای روی منجید آماده روکش ، کشیده می شود و پس از طی مدت زمان معین و با درجه حرارت بالا در پرس ها ، پخت می شود و در حین پخت نیز طرح و آج ( گل تایر) آن شکل می گیرد.
در فرایند روکش سرد ، نوار آج تایر (ترد) که از قبل ، پخت و آماده شده است ، طی فرایندی بر روی منجید قابل روکش گذاری کشیده می شود و پس از طی مدت زمان مشخص و با درجه حرارت پایین در کوره های مخصوص ( اتوکلاو) پخت می گردد.
پخت روکش گرم
در این واحد تایرهایی که به روش گرم ساخته می شود داخل قالب پرس قرار گرفته و در مدت زمان مشخصی پخت انجام می گیرد
پخت روکش سرد
تایرهایی که به روش سرد تولید می گردند ، ابتدا تیوپ گذاری و سپس اینولپ گذاری می شوند. نسبت به سایز تایر رینگ گذاری می شود . پس از پروسه تست و عدم نشتی تیوپ و اینولپ، ، تایرها داخل اتوکلاو قرار گرفته و عملیات پخت برای زمان مشخصی صورت می پذیرد.
بازرسی و کنترل نهایی
پس از اتمام کار پخت، در هردو روش سرد و گرم ، تایرها توسط واحد کنترل ، بازرسی و پس از تایید به انبار تحویل می گردد.
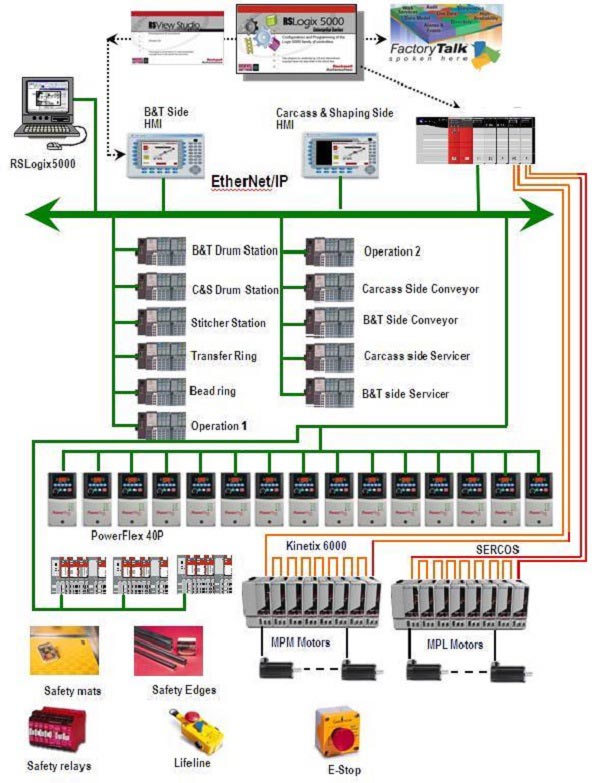
.
لیست قیمت مهندسی فرآیند تولید لاستیک خودرو
با عرض پوزش کلیه قیمت ها در حال بروزرسانی می باشد، لطفا جهت استعلام قیمت خرید با واحد فروش تماس حاصل نمایید.